The Complete Guide to SCADA Programming and How It Paves the Way for Big Data
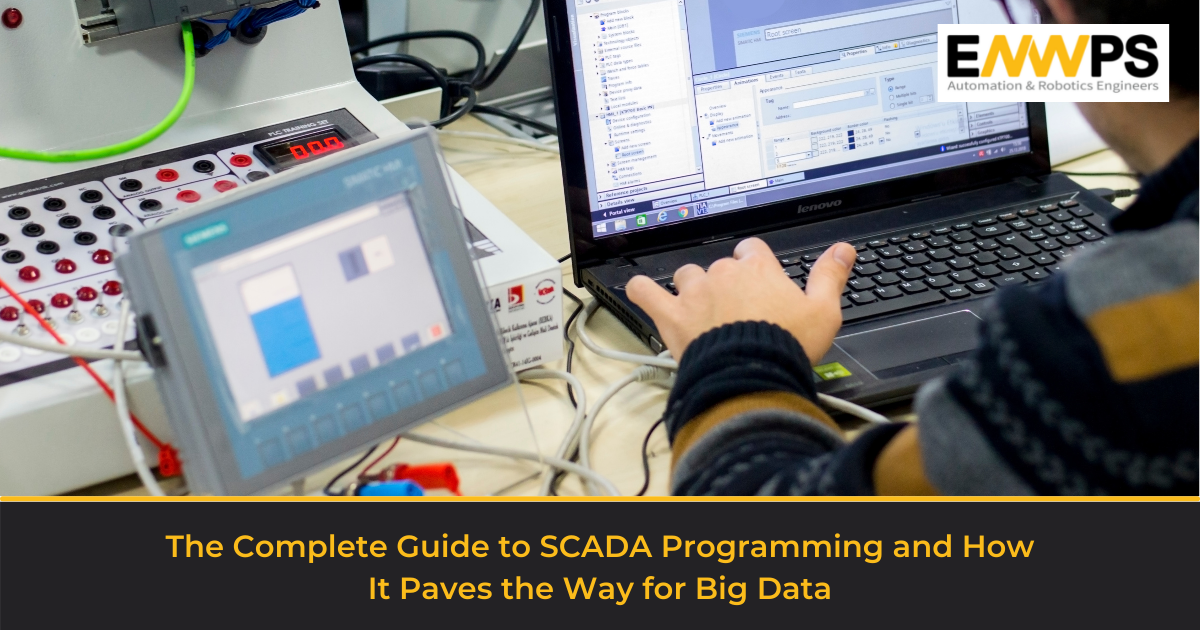
SCADA or Supervisory Control And Data Acquisition, as the term indicates, is a computer-based control system. Originally developed for industrial plants and production facilities, SCADA can be used at any place where machines and equipment need to be monitored and controlled, e.g., warehouses, utilities, buildings, etc. This is done by automating the functions of collecting, processing, monitoring and display of data gathered from the equipment through remote field devices. The system gathers and monitors metrics like pressure, temperature, flow rate, pH, etc., the values of which are compared with the defined set-points, and action is initiated to perform corrective tasks by remote control for smooth running of the plant or utility. The SCADA system architecture comprises both hardware and software elements.
How SCADA Programming Works
SCADA monitors and controls processes through field devices like sensors and relays that generate the inputs and outputs. Inputs form one of the four main components of SCADA, the other three being: RTUs or Remote Terminal Units; HMIs or Human-Machine Interface; and the Communication Network. To understand how SCADA works, one must understand how these four components work. The inputs are collected by networked devices and sensors mounted on the equipment like motors or pumps in the form of signals that contain the information like power supply, temperature, pressure, vibration, etc. Though devices and sensors generate the inputs, they cannot read or interpret them. This is done by the second component, the RTUs and PLCs, which are computerized units that acquire the site data like meter readings, pressure, voltage, equipment status, etc. The RTUs/PLCs pass on the inputs to the third major component, the HMIs that are located at the central control room where the information from the signals is displayed in readable and actionable form – graphically or through indicators – for quick response, which is again communicated through the same RTUs for corrective action through relays and actuators. The fourth major component of SCADA is the communication network, which completes the system. The four main components of SCADA thus have four corresponding functions – Data Acquisition, Data Interpretation and Action, Data Presentation and Networked Data Communication. Apart from the four main components, there are other components and tasks like the supervisory system and programming that complete the SCADA architecture.
What Benefits Does SCADA Programming Have for Big Data Integration?
Data is what is driving decision making in industry through digitalization, be it process or discrete manufacturing. This data is gathered from the entire plant or process industry operations spread across multiple locations, through field devices. IoT devices and edge computing has further enabled capturing of data that was earlier not possible to collect and monitor, giving rise to the term Big Data. If a manufacturing industry has operations spread across different locations and countries, all these can be controlled by web-based SCADA centrally, replacing various other monitoring software and devices. Mere gathering of data is of little use unless it is analyzed and contextualized, a function that SCADA facilitates. Data analytics help identify problems before they cause a breakdown resulting in costly downtime. The insights thus gathered also help plant managers to schedule maintenance and avoid unplanned downtime. These insights are also useful in better management of running equipment and avoid idle time, saving energy or improving efficiency. It can thus be observed that SCADA systems have grown in sophistication and are integrated with all data sources of equipment and operations across a wide area and multiple locations, facilitating better decision making and raising the overall equipment effectiveness (OEE).
SCADA System Architecture and Its Components Explained
First developed in the 1950s, SCADA is now in its fourth generation and increasingly powered by IoT devices. Despite this evolution, the basic components of the system remain the same, with addition of more devices, and modern digital communication systems.
The SCADA system architecture, in its most simple form, is like a tree diagram. The SCADA host is at the apex, which branches down to SCADA nodes or servers, which in turn connect to the RTUs or PLCs that are connected to the field devices, representing the tree structure.
A typical SCADA system consists of the following basic components, a mix of hardware and software:
- Human Machine Interface (HMI) – basically an input/output device, the HMI presents the information to the human operator graphically for control and action. The HMI is linked to the databases that provide all necessary data and information about system parameters, maintenance procedures, etc., which is programmable depending on the process requirements.
- Supervisory System – also referred to as Supervisory Station, this comprises the software and servers that communicate between the field equipment and the HMI software running on the control room workstations. The supervisory station comprises a single PC in smaller SCADA systems. For larger SCADA systems, it comprises multiple servers, disaster recovery sites and distributed software applications.
- Remote Terminal Units (RTUs) – these are part of the hardware, microprocessor controlled electronic devices. The RTUs that receive data from the sensors and send it to the supervisory system and in turn receive messages from the master system for controlling the connected equipment.
- Programmable Logic Controllers (PLCs) – these are alternative devices to the RTUs connected to the sensors for collecting and transmitting the input/output. PLCs have certain advantages over RTUs like flexibility, configurability, versatility and affordability.
- Communication Infrastructure – SCADA systems use various communication systems like directly wired, radio or a combination depending on requirements. Large operations spread over wider locations like utilities and process industries also use optical networks like SONET/SDH.
- SCADA Programming – this is done via standard interface and is used to create maps and diagrams that provide important information in case of an event or process failure. Programming is done by using C or other appropriate language using standard interfaces.
How SCADA Systems Operate from Development Phase to Implementation Phase
With the evolution of SCADA over the past 50 years and more, the system has become more affordable and easier to implement, yet has grown in complexity with several added functionalities. Today there is a wide choice of industry and sector specific SCADA systems in the market – off-the-shelf or customized – as also vendors for the software and hardware components should any enterprise decide to build their own. Either way, before implementing the system there are a few steps that need careful consideration:
- Clearly understanding of the process requirements
- Current data collection process
- Server for data collection points
- Additional data collection points
- Centralizing data monitoring
- Determining the software for data
- Graphical representation of data and controls, and
- Defining the level of automation and controls.
Once the SCADA system is set up with the hardware in place, it is run by the software and facilitates interaction with the plant or process facility. The HMI display shows the running status of all the field equipment, and issues alerts and informs maintenance schedules, etc., as programmed.
Conclusion
SCADA system is one of the most commonly used industrial control systems to manage most types of industrial process. Though seemingly simple, a modern SCADA system is complex in operation. The choice of the system – off-the-shelf or customized – needs careful consideration as there are pros and cons. An off-the-shelf system is faster to deploy than a customized one, but sometimes a customized system makes better sense. Professional expertise can help ease the pain points in implementing SCADA for any given operation. Pune based ENWPS has the necessary domain expertise and experience for helping companies build and operate SCADA systems of any size and scale. Its experts can help in system selection and implementation, programming, and maintenance to ensure a trouble-free operation.