Automated Manufacturing with Robotics, AI and Data-Driven Production
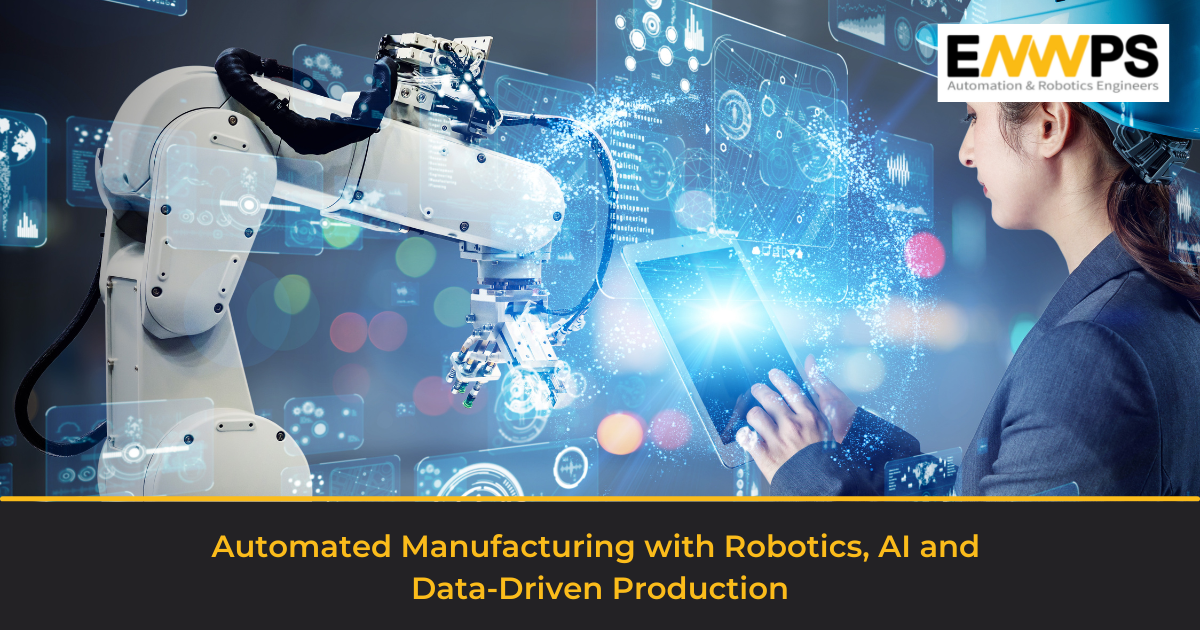
Automation has already removed the drudgery from the manufacturing process. The automotive industry is a popular example of how automated assembly lines in conjunction with robotic welding and painting shops are rolling off on an average 120 cars a day from a typical plant. While the automobile industry is an early adopter of automation, today Industry 4.0 is ushering in a new era of digitalization where decisions are driven by the data analyzed in real time to further automate manufacturing with the help of intelligent robotics. The ultimate goal of the entire concept of Industry 4.0 is autonomous manufacturing in factories of the future, with minimal human intervention.
How AI-Powered Robotics is Transforming Manufacturing Today
The digital transformation of manufacturing goes hand in hand with the combination of robotics and a host of digital technologies – most notably smart sensors – with artificial intelligence (AI) and machine learning (ML) as the cutting edge. Conventional robots used in the manufacturing industries for the last several years had limited capabilities in terms of movements and nature of operations, though they are highly efficient in operation for mass production, for jobs like welding, painting and pick and place. AI-powered robots, on the other hand, are equipped with a wide variety of sensors and are ideal for performing many more tasks like assembly of precision parts and components, inspection of parts and components for flaws and defects, and sorting and packing of finished products. These AI-powered robots are data driven, the data collected from a host of sensors either integrated inside the robots or placed strategically in the operations area from where they provide highly accurate measurements for precise movement control and accurate monitoring of the process. These new generation robots are automating tasks that were so far from the preserve of human workers and performing them with much more efficiency and high accuracy. A robotic workforce is now ready to take over more and more functions on the shop floor, leaving human workers free for more creative jobs and pursuits. This also goes well in the advanced economies where robots are making up for a dwindling workforce. The future of manufacturing is linked closely with the future of robotics.
How Robotics and AI in Manufacturing has Changed
The robots of the previous generation basically automated routine and repetitive tasks, and were mounted in fixed positions. These were highly suitable for mass production where day in and day out, the same models of cars or the same type of white goods were manufactured. The present trend of flexible manufacturing usually means more customization, smaller batch sizes, and different types of products manufactured on the same assembly line, with the changes effected in machines and robots via programming alterations. The assembly line itself has changed in many cases and made way for manufacturing cells in smaller configurations more suited for flexible manufacturing, where AI-powered robots have taken over more and more tasks from their human counterparts. These are collaborative robots that are free from safety cages, are smaller, more agile and mobile, often mounted on autonomous guided vehicles (AGVs), moving unobtrusively around the shop floor. Thanks to artificial intelligence, these robots are not only easy to program and self learn, but they also teach other robots, saving time and human resources. They have better architecture and more computing power and data storage capacity, which make them ideal for more autonomous operations, towards realizing the goal of smart factories. The outlook for robotics, vis-à-vis the role of robots in manufacturing, is thus very positive. While there are many pros of robots in manufacturing, one cannot ignore the flip side. The few cons of robots in manufacturing include the high initial investment. But globalization also means that unless manufacturing is competitive with respect to the more advanced economies, developing nations cannot find their rightful share in the market.
The 2 Things That You Must Start Doing to Remain Competitive
The world of technology is constantly evolving and so is the manufacturing process. This evolution of the manufacturing industry is evident in the implementation of AI and Robotics. There are many things manufacturers can start doing if they must remain competitive, but if one has to name just two, these should be:
- Know your consumer; and
- Innovate and adapt.
Understanding consumer likes and preferences is a key to success in business. This is easier said than done because often the masses either have unlimited wants and needs, and are unable to meet them. An astute businessperson is one who finds a way to meet some of these needs at optimum cost and cater to the requirement anticipating what the consumer really needs.
The second, and more important thing, is to innovate and adapt to the latest trends in manufacturing, in order to make the product most economically and efficiently, without compromising on quality. This is possible only with the use of latest technologies, and in the case of manufacturing, use of automation and robotics.
The Benefits of Implementing Data-Driven Manufacturing Practices
Data has often been compared to oil or gold, which are high value commodities, indicating the importance of data. Manufacturing being a high risk, capital intensive business should always be based on data derived from various sources. In the digital era, smart and affordable sensors in conjunction with the Industrial Internet of Things (IIoT) have made data capturing easy, but not all enterprises have succeeded in making use of this data, which is humongous and unstructured at the source. Use of artificial intelligence in data analytics helps in getting the structured data, which is further refined by applying machine learning algorithms. Once implemented, data driven manufacturing has several benefits that come with better planning, enhanced productivity and optimization of resources, besides better maintenance practices that prevent unexpected downtime.
The Benefits Can Be Summarized Thus:
Greater transparency: Structured data clearly brings out the facts of the entire process offering better visibility, discovering bottlenecks and exposing inefficiencies and poor maintenance practices, helping a better understanding of the situation by all stakeholders, which also instills accountability.
Improvement and innovation: Better visibility of the process of manufacturing automatically leads to continuous improvement to overcome the drawbacks, and promotes innovation to overcome the difficulties, incentivizing performance as well as engendering a competitive spirit among the workers as the metrics are now measured and monitored.
Predictive maintenance: With better data analytics, it is easier to implement predictive and prescriptive maintenance practices based on machine monitoring and anticipating failure, which avoids unexpected downtime. Maintenance schedules can be planned in advance to avoid stoppage of work during busy production schedules.
Faster decision making: Insights gained from data analytics helps in making quick decisions about inventory planning and streamlining of supply chain with further optimization of resources, that avoids both – sudden running out of parts and components as well as pile up of surplus inventory. With faster decision making, organizations benefit from quick order fulfillment and better customer satisfaction.
Cost reduction: Lessons derived from data analytics help streamline the total production process that eliminates inefficiencies, optimizes manpower with more automation, and minimizes waste. With incremental measures like these, production efficiency increases resulting in overall cost reduction, also improving product quality in the process.
Conclusion
With all the available resources today in terms of data gathering and analytics, there is little surprise that the future of manufacturing will be data-driven. As analytics get better with AI and ML working in tandem to further improve the predictions and increase transparency, manufacturing industries stand to gain the most. This would be achieved by following a three-pronged approach: deriving actionable insights; predicting future outcomes; and enabling self-optimizing systems for autonomous self correction. However, there are some critical challenges in the process, especially when it comes to legacy plants and organization cultures that still follow the siloed approach preventing information sharing. Another area is system security and the growing cybersecurity concerns with the proliferation of IIoT devices that are vulnerable to hacking. These are the areas that need professional expertise and enterprises must be willing to seek help from the right quarters.