How PLC Programming Can Help Scale Your Manufacturing Business
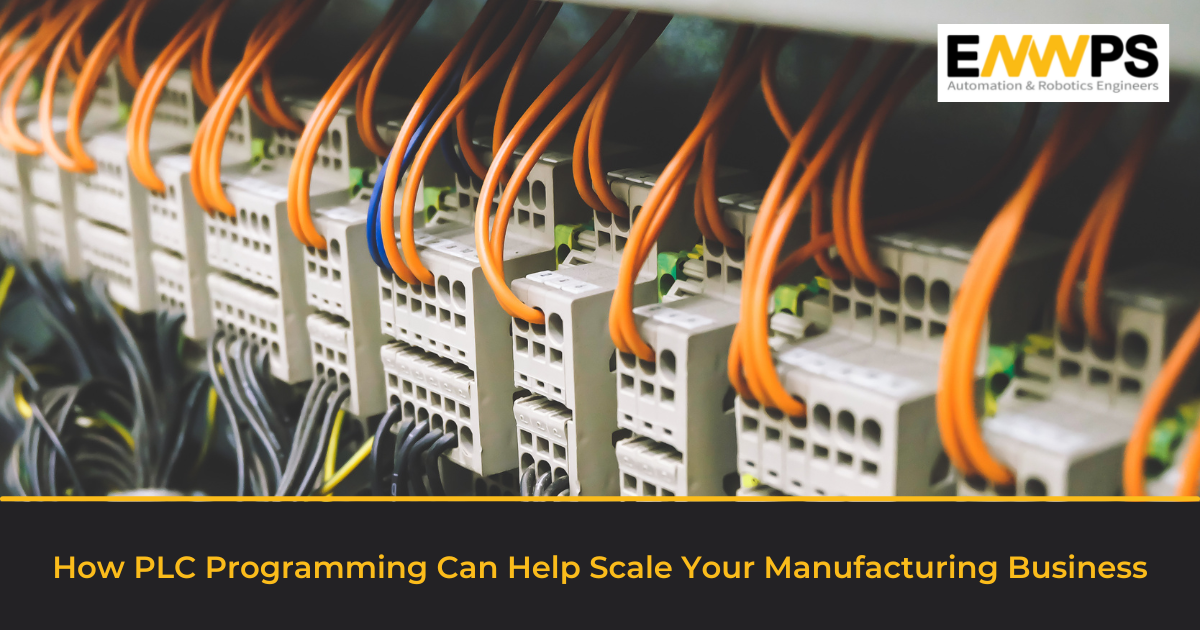
A PLC – Programmable Logic Controller – is a tiny, rugged computer used in industrial automation. Though the CPU of the PLC is not as versatile as the one used in PCs for regular use, it is extremely fast for the tasks it is designed for, and unlikely to slow down in operation. The key to successful automated plants or process industry operations is in programming the PLC correctly. The 5 languages popularly used for PLC programming – Ladder Diagram, Sequential Function Charts, Function Block Diagram, Structured Text and Instruction List – are all part of the IEC Section 61131-3 Standard. This IEC Standard allows some ground rules that standardise PLCs and their languages. Each language has its pros and cons, and some PLC manufacturers have also evolved their own language for their PLCs. The programmer must be familiar with the PLC program syntax – which is how the program is written, the codes and the symbols used. An incorrectly programmed PLC can result in costly downtime and can even cause damage to the equipment or the plant.
How PLC Programming Can Help Scale Your Manufacturing Business
PLCs have been in use in industrial automation for over 50 years and have proved to be cost-effective and reliable in automating systems and processes. Before the PLCs, industrial machines were controlled by a huge array of relays, hardwired in a very specific way. PLCs replaced the cumbersome relay system with electronic solid-state control. A modern manufacturing plant comprises several machines that form an assembly line or a manufacturing cell, each having a specific role or function, and operate in a sequence to complete a cycle of operations. For example, a piece of sheet metal may pass through a cutting machine first, before entering a bending machine and then go to the drilling machine and end up with a grinding machine to metamorphose into a panel for mounting switches. This is an automated operation where the part moves through four machines automatically through conveyors without any human intervention, getting cut to size, bent at certain angles, holes drilled at appropriate places and finally rough edges are ground smooth. This entire operation is facilitated by the PLC, which has been programmed to follow the sequence and the time cycle, based on the trials taken to perfect the sequence. This process of automating production is what helps industries scale up their manufacturing business, by applying it to each machine and function, the machines together forming the production cell or assembly line.
How PLC Programming Can Help Automate Certain Processes
A typical manufacturing unit today is a combination of human efforts and mechanization. For example, in automobile manufacturing, the assembly of individual parts like engine and gearbox may involve human labor, but operations like the welding of the chassis and painting of the car after assembly are mechanized and fully automated. These tasks are performed by robots, which are also synchronized to perform in the desired sequence through PLCs. Increasingly, artificial intelligence or AI plays a role in such complex tasks. The role of AI in manufacturing is on the increase, as it becomes more data driven, the data collected during machine operation and analyzed to gain more insights. These insights help optimize the processes further.
Today most processes in the manufacturing industry can be automated by using a series of workstations linked by a transfer system operated by robotics and control systems. It must be understood that repetitive tasks are mostly automated, and the sequence of operation is well known and understood, which forms the basis for programming of the PLC. Each workstation performs a specific operation, and the product moves forward progressively until the task is completed and the final product is ready. For example, in a bottling plant, empty bottles are picked up automatically from the crate, arranged on the conveyor system where they are first washed automatically at one workstation, dried at the next, filled with the appropriate content, capped, labelled and finally loaded in crates, ready for dispatch, without any human intervention. All these are repetitive operations, and can be programmed in a PLC, which receives signals from input devices, such as sensors and switches, and based on the logic program, activates output devices like motors or other machinery. The role of human workers in such an environment is to just supervise and monitor the operation and intervene only in case of sudden stoppage of the machine, to initiate corrective action.
PLC Programming: The Key to Better Manufacturing?
The PLC is at the heart of the automation system in the manufacturing environment and programming determines how it works in operation. This means PLC programming is the key to better manufacturing. The PLC basically has a few important components – the CPU, I/O modules, rack and power supply. The CPU is the brain of the PLC which does all the calculating and works at an extremely high speed. The I/O or input/output modules connect the field inputs (basically sensor data) and outputs (signal for devices that produce actions for movement of machinery). The rack facilitates the data exchange between the CPU and the I/O modules, and the power supply does what the name suggests – provide energy. Programming is what makes this entire operation work in a predetermined sequence – read the machine parameters, provide the inputs, and based on the operational requirements, and let the CPU take corrective measures that are transmitted as output for appropriate action. Parameters like temperature, pressure, speed, etc., of the machinery are thus controlled and kept within specified limits for safe and trouble-free operation without any stoppage or breakdown. There are hundreds of such operations performed in a typical manufacturing plant, and the programming of the PLC is what keeps the plant running smoothly which in turn facilitates better manufacturing operations.
Pros and Cons of Outsourcing your PLC Programming Projects
More and more companies today are automating their operations. Apart from new factories and manufacturing plants that start with automation, almost all legacy plants are also undergoing modifications and upgrades, automating many if not most operations. This has resulted in great demand for software and coding specialists, and consequently creating the need for outsourcing certain requirements. PLC programming is a skilled task and involves hours and hours of coding, which is getting even more complex in the age of IIoT and connected plants, with data driven decision making and use of artificial intelligence and machine learning algorithms. So what are the advantages and disadvantages of outsourcing such a critical task?
One of the main benefits of outsourcing is that companies get a depth of expertise that is rarely available in-house, and even if one tries, such talent comes at great cost, which the volume of work may not justify. Outsourcing companies are staffed by experienced industry professionals at the top, and programming experts at other levels, a combination which makes for swift execution, which together with the cost advantages works highly in favour of the company. The trend of outsourcing is not new; it has been perfected over the last two decades so today the outsourced companies understand the product development cycle. Backed by their experience of doing similar tasks over a long period, they also understand the users’ needs and are able to deliver what is exactly asked for. Moreover, today the cost of communications is minimal and modes multiple, so remaining in constant touch to resolve issues as they arise is no longer a problem. Companies large and small can benefit from outsourcing in view of these advantages.
There are of course some disadvantages in outsourcing, the foremost being the risk of cybersecurity breaches and compromising the intellectual property. Not all outsourced organizations have the professional integrity to allay all such fears. The other major concern – poor quality of work – often results from wrong choice or inadequate checks during due diligence. One should however be cautious when outsourcing about the cost, and insist on transparency on that front, lest there be hidden costs which could make the project very expensive! Also, not many outsourced companies have the credentials to undertake challenging tasks. A little less common, though by no means negligible, is the problem of cultural incompatibility in the age of globalization, where certain geographies may be less amenable to sharing such working relationships.
Conclusion
Successful businesses today are thriving on automation and more automation. The Covid pandemic and the resultant lockdown that shut down most businesses also brought home the fact that those businesses that were high on the automation adoption curve could face the lockdown with lesser disruption, with minimum manpower. Automation in the manufacturing business relies on machines, which in turn are operated with the help of PLCs. As more and more businesses choose automation to run their production lines, PLC programming will be their critical link to improved productivity. However, companies that are just embarking on their automation journey may well tread cautiously, and consult with professional agencies, both about the feasibility of going in for automation, and the ways to implement it. In an era of specialization, it is difficult for enterprises to have all the talent in-house. Automation, robotics and digitalization are words often used today, but not all businesses can profit from the high capex that these technologies need. At the same time, it is not possible to scale up without adopting modern methods. Professional expertise can guide companies in this endeavour.