How PLC Programming Can Improve Plant Efficiency and Productivity
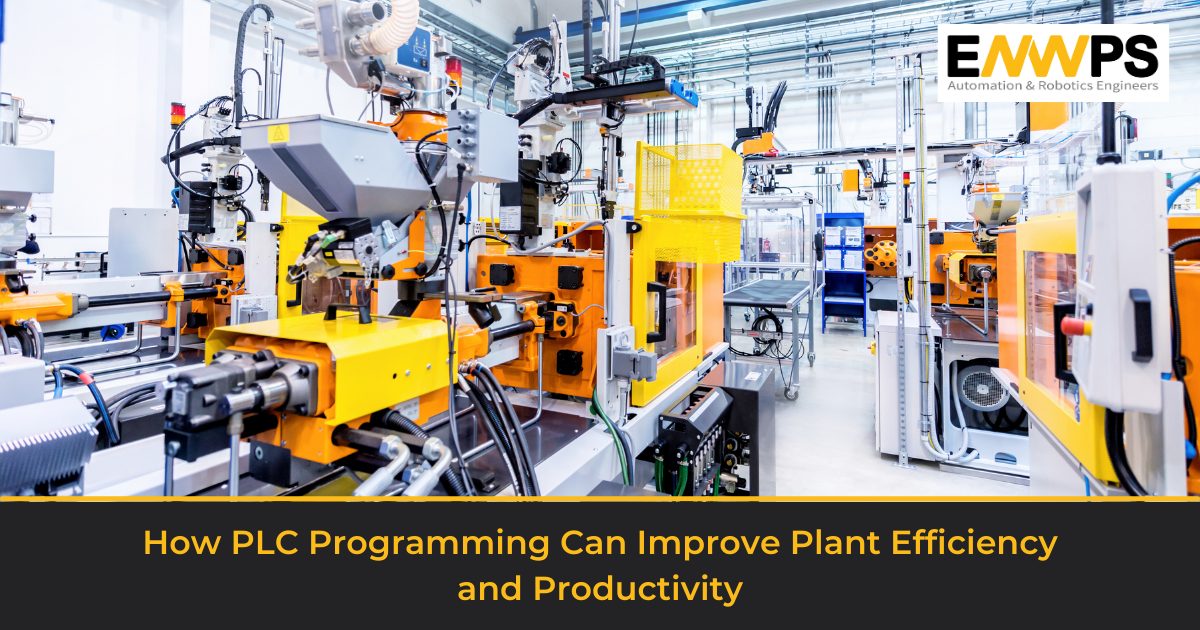
PLC programming is a powerful tool that can significantly improve plant efficiency and productivity in today’s competitive industrial landscape. By leveraging the capabilities of Programmable Logic Controllers (PLCs), manufacturers can streamline operations, optimize processes, and unlock new levels of operational excellence. In this article, we will explore how PLC programming empowers manufacturers to drive efficiency, productivity, and growth in the modern industrial environment. Let’s discover the transformative impact of PLC programming on plant operations.
Defining PLC and its Importance
A PLC is a digital computer used for the automation of various electromechanical processes in industries. PLC consists of a microprocessor which is programmed using the computer language. They are designed to perform specific tasks by executing pre-programmed instructions and logic. Their importance lies in their ability to provide precise and reliable control over industrial processes, ensuring efficient and consistent operation. PLCs play a crucial role in improving safety, enhancing productivity, optimizing resource utilization, enabling flexible manufacturing, and facilitating integration within the industrial ecosystem. With their flexibility, scalability, and advanced features, PLCs are an indispensable component of modern industrial automation systems.
Benefits of PLC: Efficiency, Productivity, Safety
PLCs offer several benefits when it comes to improving plant efficiency and productivity. They can be programmed to control complex processes with high precision and accuracy, reducing the risk of human error and increasing overall efficiency. They can also help improve safety by monitoring equipment and processes for potential hazards.
Key Components of a PLC System
A typical PLC system consists of several key components, including a central processing unit (CPU), input/output (I/O) modules, power supply unit, programming device, and communication interface.
PLC Programming Steps: Design, Testing, Implementation
The process of programming a PLC involves several steps, including design, testing, and implementation. During the design phase, the control logic is developed based on the requirements of the process being automated. This logic is then tested using simulation software to ensure that it performs as expected. Once the design has been validated, it is implemented on the PLC hardware.
Case Studies: Examples of Improved Efficiency and Productivity
There are many examples of companies that have successfully implemented PLC systems to improve their efficiency and productivity.
Due to manual procedures and obsolete equipment, a large food and beverage company was experiencing production line downtime. To increase productivity and decrease downtime, they required a solution. A PLC system was put in place by the business, automating the production line and enabling real-time monitoring of the machinery and procedures. As a result, downtime was cut in half and production efficiency rose by 20%.
Future of PLC: Advancements in Technology
The future of PLCs (Programmable Logic Controllers) is poised to witness remarkable advancements driven by rapid technological developments. As Industry 4.0 continues to evolve, PLCs are expected to become even more intelligent, interconnected, and capable. Advancements in technology will enable PLCs to handle increasingly complex tasks, integrate seamlessly with other devices and systems, and leverage emerging technologies such as artificial intelligence (AI), machine learning (ML), and edge computing. This will lead to enhanced automation, real-time data analysis, predictive capabilities, and adaptive manufacturing.
PLCs will play a pivotal role in creating smart factories, where interconnected systems collaborate efficiently, optimizing production processes, improving quality control, and enabling responsive decision-making. Moreover, advancements in cybersecurity measures will be crucial to safeguard PLCs and the connected industrial ecosystem against evolving threats. The future of PLCs promises to revolutionize industrial automation, driving efficiency, productivity, and innovation in manufacturing processes.
Conclusion
In conclusion, PLC programming is an essential tool for improving plant efficiency and productivity. By implementing a well-designed PLC system, manufacturers can reduce costs, improve safety, and increase their competitiveness in today’s fast-paced market. If you’re looking for extraordinary manufacturing success, then choosing the best ones in the market for all your PLC requirements will drive your business to it. Choose ENWPS today!
Talk to us today! Reach us on automation@enwps.com