How to Program a PLC: A guide on how to get started programming a PLC and HMI
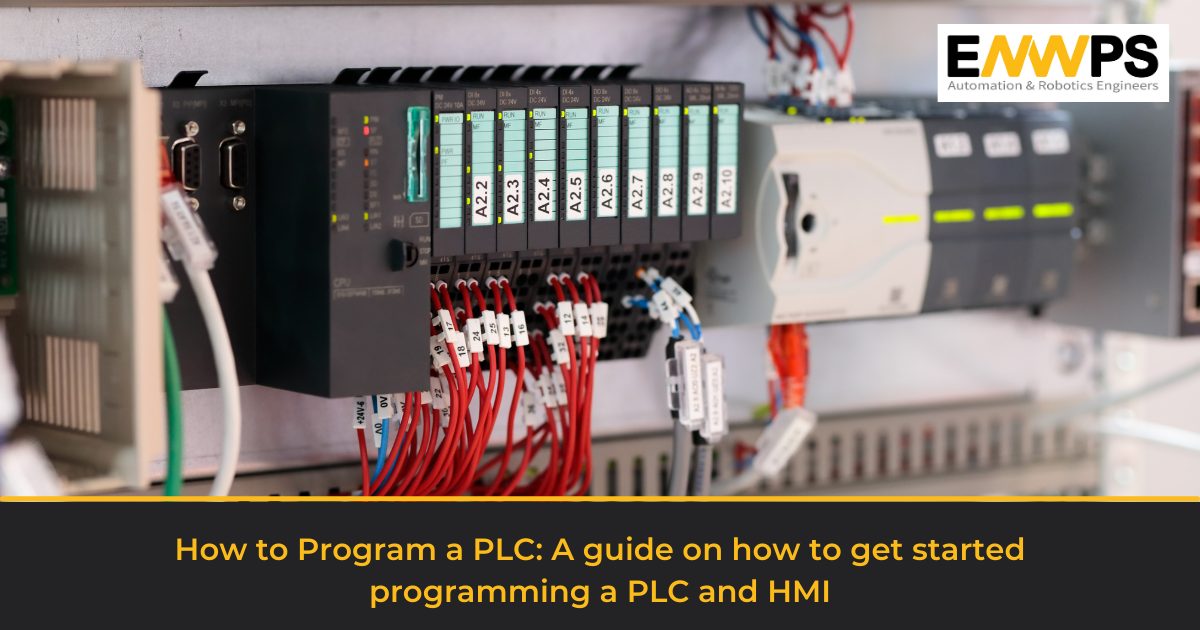
HMI, or Human Machine Interface, is growing its presence and is entering our daily lives in the most silent way possible. You might not realize, but we are already using an HMI every day. The best example of that is bank ATMs. You can use the machine to dispense a certain quantity of money or to deposit money using the screen and push buttons. In an industry, HMIs play a more significant role by enabling personnel to monitor machines and operate them in an automated way. But how can we couple PLC and HMI, and how has it benefited the process of automation and increased efficiency? Let’s decode them one by one, starting with a PLC overview and an HMI overview. Let’s dive in:
What is PLC?
A ruggedized computer called a PLC, or programmable logic controller, is used in industrial automation. These controllers have the ability to automate a particular procedure, a machine feature, or even a whole manufacturing line. PLCs are helpful instruments for repetitive operations because they can collect data and don’t have any mechanical parts.
What is HMI?
A Human Machine Interface, or HMI for short, is a tool that enables a human to communicate with the PLC managing the manufacturing process and receive feedback from it. In other words, it is a way for you to instruct your devices and receive updates on their progress.
How to Program a PLC?
For the purpose of debugging and increasing efficiency, many HMIs may also link to PLC logic and display it on the screen. Compared to constantly connecting a computer or laptop, this can save significant time and effort. Together, HMIs and PLCs monitor and manage the machine. This implies that they must get along and, in a sense, speak the same language.
There are five easy steps to program a PLC to achieve the highest efficacy and for the HMI and PLC to be able to communicate with each other:
- Define the task
- Define the inputs and outputs
- Develop a logical sequence of operation
- Develop the PLC program
- Lastly, test the program
Once you’ve tested the PLC and added the required commands, all you have to do is establish a viable connection between the PLC and HMI so that the data is ready to be displayed. This is achieved by doing it on a “protocol.” Modbus, Ethernet/IP, and Profibus are popular protocols. All of these are just industrial networks, which can be easily found on each manufacturer’s website. After that, anything that is programmed into the HMI can be used to monitor and control PLC functions.
Why is it Important to Program a PLC?
PLC programming has enabled industry operations to work seamlessly and monitor machines with more efficiency. Here are the reasons why it is important to program a PLC:
- Improves accuracy and reliability and reduces system malfunctions.
- PLCs are capable of a wide range of complicated jobs that PC systems cannot.
- PLCs make it possible for you to spend less time and money upgrading or updating hard drives while also better preparing for your charter.
- They simplify vessel monitoring and work at lightning speed.
HMI vs PLC: What are the differences?
There are some significant differences between HMI and PLC programming, which set them apart and enable companies to best utilize them. Here are the key differences between HMI and PLC:
- In a PLC, the logic must be written, whereas, in an HMI, the logic view must be designed.
- In contrast to PLC, where the parameters must be configured in order to perform the programme, HMI allows you to adjust and monitor the settings.
- As opposed to working with libraries, hardware configuration, network setup, and other advanced tools in PLC, you can design and use audit trails, reports, trends, printouts, and other advanced tools in HMI.
- The HMI can be compared to the eyes and the PLC to the brain.
Conclusion
HMI-PLC combo units are advantageous for more straightforward applications because they are less expensive, require less time to design, and occupy less panel space. The separate PLC and HMI solutions will improve efficiency and accuracy and leave little to no room for system malfunctions, saving you money and reducing stress.