Programmable Logic Controllers (PLC): The Concept and Benefits of PLC Programming
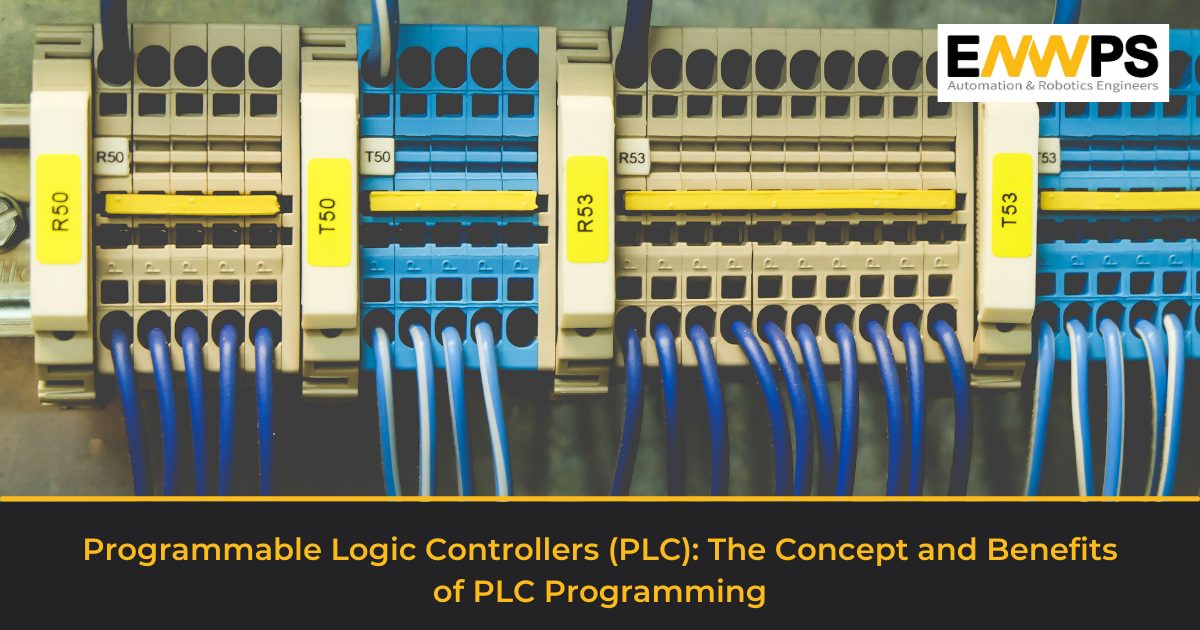
Programmable logic controllers (PLCs) are a type of computer system used to automate and control industrial processes. They are designed to be easy to program and offer numerous advantages over traditional hardwired systems. They are used in a wide range of industries, from manufacturing to robotics, and provide many advantages over conventional hardwired systems. Let’s discuss the advantages of PLC programming, the components of a PLC system, and the benefits of PLC programming. With the help of this blog, we will also explain the concepts and benefits of PLC programming.
What is PLC Programming?
The process of developing internal logic for a programmable logic controller is known as PLC programming (PLC). PLCs are often programmed in a “language” exclusive to the controller; this translation from spoken word to something the controller can understand and execute is correctly explained.
The primary purpose of a PLC is to provide a reliable and efficient means of controlling and monitoring automated processes. It is a computer-based system that uses a series of instructions to control the operation of a machine or process. It is designed to be a cost-effective and reliable alternative to hardwired systems. PLCs are used in a variety of industries, from automotive and aerospace to food and beverage manufacturing.
Advantages of Using PLC
There are many advantages to using a PLC system in industrial automation and control. The main benefits of PLC programming include the following:
- Increased efficiency, improved safety, and greater flexibility.
- Easy to program and capable of performing complex operations with minimal effort.
- They can also be programmed to execute sequences of instructions, allowing for more complex tasks to be automated.
- The programming code is stored in the PLC, making it easy to update the instructions.
- Provide a greater level of safety than traditional hardwired systems.
- They are robust and reliable, meaning they are less likely to fail than traditional hardwired systems.
- PLCs offer greater flexibility than traditional hardwired systems. This allows them to be used in a variety of different applications.
What are the Components of a PLC System?
The main components of a PLC system include a
- Programmable logic controller,
- Input/output interfaces,
- Power supply, and
- Programming software.
How do PLC Systems Work?
The PLC itself is the main component and is responsible for taking input from sensors and executing the instructions programmed into it. The input/output interfaces allow the PLC to communicate with external devices such as sensors, switches, and relays. The power supply provides the electricity needed to operate the PLC. Lastly, the programming software is used to create the instructions that the PLC will execute.
The PLC can be programmed using a variety of programming languages, such as ladder logic, function block diagram, sequential function chart, structured text, and instruction lists. Each of these languages has its own advantages and disadvantages, so it is crucial to choose the language that is best suited for the task at hand.
Conclusion
If you are looking to improve the efficiency, safety, and flexibility of your industrial automation and control processes, PLC programming is a great option. With the right PLC programming services, you can unlock the full potential of your PLC system. Needless to say, PLCs have transformed automation in industries and are constantly evolving. As technology evolves and add newer versions of connectors, software and hardware, PLCs have the flexibility to adapt and update. While everything around is changing, keep in mind to choose an appropriate PLC programming service that serves your purpose well and gives you an upper hand.