The Building Blocks and Essential Characteristics of a Smart Factory
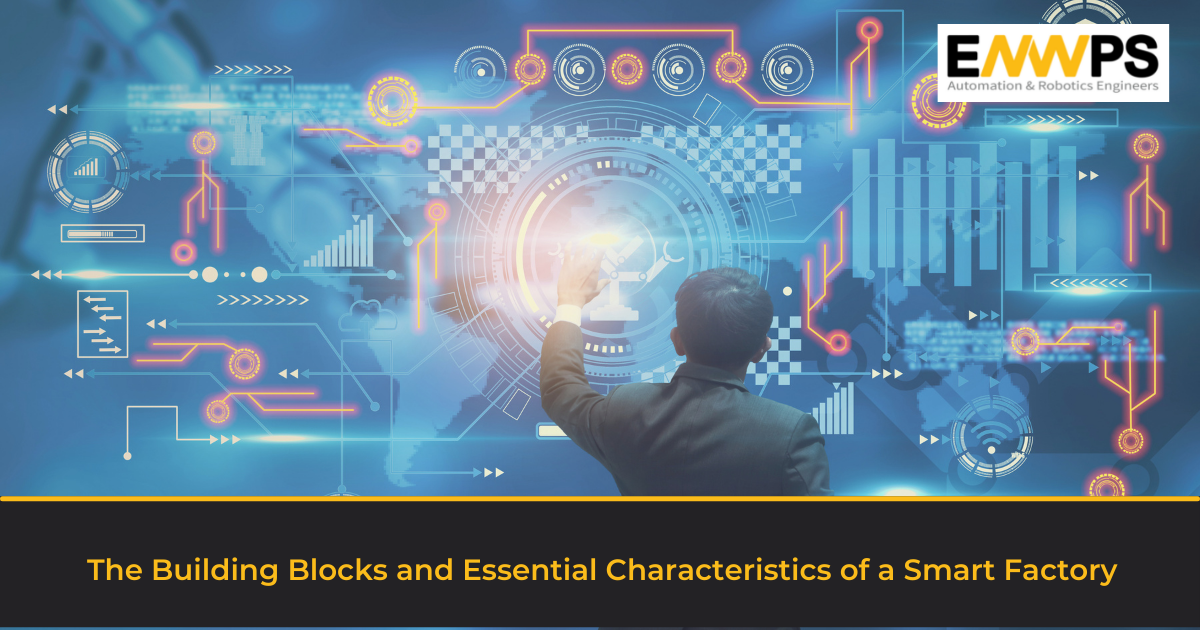
Introduction to Smart Factory
With the advent of the industrial internet of things (IIoT), digitization, automation robotics, big data analytics, artificial intelligence, and the concept of interconnectivity in the manufacturing ecosystem, facilities are gradually transforming into smart factories. A Smart facility combines production processes and operations with a digital network of connected devices and machinery. It goes beyond simply automating the production processes. At a broader level, it maximizes the performance of the enterprise by extending the capabilities of machines to respond in real-time to meet changing conditions in the facility and demands of the consumers without human intervention. The smart factory/plant technology enables flexibility in the manufacturing system allowing evidence-based optimization of the processes, assembling real-time data, and providing control of the overall system to independently run production processes.
Smart Factory Technology
Smart factories accumulate a variety of equipment and devices to streamline and optimize manufacturing processes. The interactions and combinations of diverse smart factory technologies contribute to the transformation of a factory into an intelligent workplace. Below are some key technical requirements of a smart factory setup.
- Industrial Sensors: They are interlinked to industrial machines, devices, and processes for allowing the exchange of information between machines and humans for optimizing shop floor operations. Various types of sensors are deployed according to the required output. For instance: temperature sensors, pressure sensors, level sensors, proximity sensors, optical sensors, etc., each one has distinct utility in the industrial setup.
- Cellular 5G/LTE: The modern industrial cellular networks are the substitution to wired Ethernet traditionally used in industries. It allows operators and factory managers to communicate with ease inside the factory premises and from distant locations outside the factory. Cellular 5G/LTE offers mobility, ease of use, reliability, higher bandwidth, and low latency, ensuring smooth machine-to-machine and machine-to-human communication for unleashing the true potential of the industrial assets.
Related Blog: Digital Transformation Will Drive IoT and 5G development
- Industrial Internet of Things (IIoT): It is one of the key components in a smart factory that includes a combination of various information and operations technology devices to collect valuable data, analyze it, exchange across machines and operators, and improvise it for generating higher output.
- Cloud Computing: Cloud computing is demand-based accessibility of system resources, databases, servers, process information, and all relevant data from shop floor devices to make real-time, data-driven decisions and alterations in the manufacturing process. It also aids in the collection of information about supply chains, logistics, delivery services, and other operations in the industry.
- Data Analytics: The sheer amount of data generated by industrial systems and processes can help in innumerable ways. Detection of error patterns, spotting underperforming systems, insights about the production process, improving and controlling quality based on historical data, predictive maintenance analysis, etc. all can be monitored and optimized with help of data analytics.
Characteristics of a Smart Factory
For any factory to be transformed into a smart factory, the following attributes of smart factory technology need to be addressed and included.
- Interconnectivity: The prerequisite of a smart factory is to connect all the machines, devices, systems, and processes to produce real-time data that can be used for decision making.
- Optimization: A optimized factory is self-sufficient in making decisions about the ongoing operations to enhance operational efficiency with minimal human intervention.
- Proactiveness: The ability to anticipate and act before the actual problem arises and hampers the system efficiency is associated with the proactiveness of a manufacturing unit. It not only increases uptime but significantly impacts the accuracy, quality, and costs involved.
- Transparency: From real-time data visualization to transforming them into actionable insights, defines the transparency of an industrial unit. It allows operators and managers to view real-time machine/system performance, take steps to improvise, and accelerate progress.
- Nimbleness: Scalable industry layout, adaptability to changes in a working environment, deviations in production schedules, the introduction of new products, etc. with minimum manual assistance is one of the key features of smart factory automation.
Why do industries need to shift towards Smart Factory?
The market analysis states, the Global Smart Factory Market was valued at USD 270.74 billion in 2020, and it is expected to reach USD 422.88 billion by 2026, registering a CAGR of approximately 9.33% during the forecast period (2021-2026). The underlying reason is, smart manufacturing can amplify the output while significantly reducing the production costs. Below, we have gathered key reasons to help you gauge the benefits smart factories offer.
- Machine-Driven Data: Gone were the days when operators had to manually create a tabular sheet for gathering all production data and checking production efficiency. Inventory management, asset tracking, delivery planning, and all other managerial tasks were conducted manually. Today, with help of business intelligence tools, the unstructured data is collected and processed into lucid formats for better data visualization and powerful analysis. It allows manufacturers to make better decisions for optimizing the facility’s performance.
- Productivity Enhancement: Any industry irrespective of size, constantly looks for opportunities to increase the gross profit margins and reduce operational costs. Smart factories provide complete visibility of assets through interconnected systems, provide smart insights, spots bottlenecks in the process if any, reduce wastage, and self-optimize for improved process efficiency.
- Production Flexibility: It refers to adaptability, agility, and improved responsiveness of the manufacturing setup to administer product enhancement and consumer demands. With the rise of breakthrough technologies, like integrated production management systems, factories are becoming more intelligent allowing the highest level of manufacturing flexibility and customization of the products.
- Benefits of Digital Transformation: The usefulness of deploying smart manufacturing solutions includes improved production scheduling, product development, quality control, logistics management, planning machine maintenance, keeping a track of machine downtime, increasing uptime, and strengthening overall plant productiveness.
Upgrade with ENWPS
Smart manufacturing heavily relies on the digitization and connectivity of the industry ecosystem. It provides greater accessibility of data to make intelligent moves, ultimately adding up to the performance capability and profit gains of the business. The solutions that smart factory technologies offer have become indispensable for modern manufacturers if they wish to remain competitive and satisfy modern customer demands. At ENWPS, our team of qualified engineers possesses the required knowledge and expertise to help you upscale to smart manufacturing. Our services encompass supply, installation, and commissioning of the various equipment required for optimizing manufacturing processes.
Elevate your business with expert assistance! Shoot an email at: rfq@enwps.com!