The Importance of PLC Security and How to Protect Your Control Systems
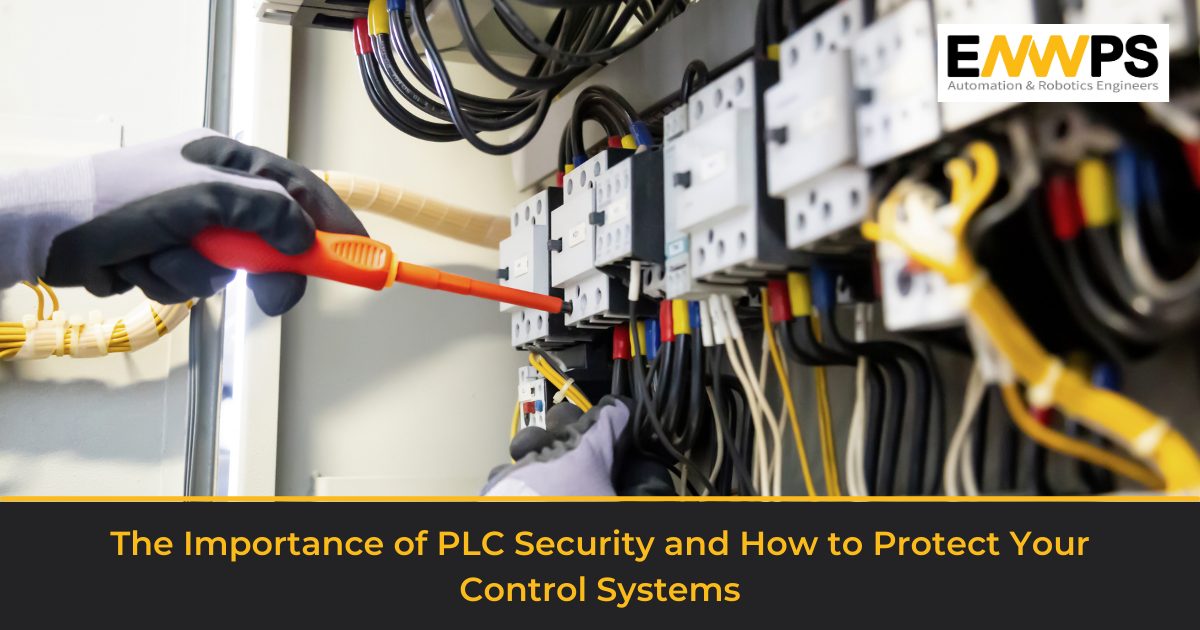
Programmable Logic Controllers (PLCs) are essential components of modern industrial manufacturing. They bring flexibility, reliability, and ease of use to standalone factory environments. Originally conceived for the auto manufacturing industry in the 1960s to replace hard-wired options such as relays, PLCs are now ubiquitous in the manufacturing industry. Since their importance in industrialization is no longer a secret, understanding the need for protecting your system is the next crucial aspect. Let’s look at how PLC Security plays an important part in protecting your systems in detail:
Explaining PLC and its importance
A PLC is a user-friendly microprocessor-based specialty computer that carries out control functions, many of which are of high levels of complexity. They are engineered to endure harsh and strenuous situations such as heated, cooled, and even moist environments. Used for automation usually in the industrial electromechanical space, PLCs are the best solution for establishing communication, monitoring, complex automated operations including temperature control, conveyors, robot cells, and other operations.
While PLCs are making automation easy and saving time and resources during regular industrial operations, we need not forget that they are equally susceptible to threats and require good-grade security in order to maintain smooth functioning.
Threats to PLC security:
There are several potential threats to PLC security, including cyber-attacks, insider threats, and system errors. These threats can compromise the safety, quality, or efficiency of industrial operations.
Unauthorized Access: Unauthorized individuals gaining physical or remote access to PLCs can manipulate or disrupt their operation. This can be through stolen credentials, weak authentication mechanisms, or unsecured network connections.
Malware and Cyber Attacks: PLCs can be targeted by malware, such as viruses, worms, or ransomware, which can disrupt their normal functioning or steal sensitive information. Cyberattacks specifically designed to target industrial control systems, like PLCs, can exploit vulnerabilities in the software or network infrastructure.
Insider Threats: Malicious actions or unintentional errors by authorized personnel can pose a threat to PLC security. It could be due to disgruntled employees, insufficient training, or lack of awareness about cybersecurity best practices.
System Errors: System errors, including software bugs, configuration mistakes, or hardware failures, can have a significant impact on the security of PLCs. These errors can result in unintended behaviors, system crashes, or vulnerabilities that attackers may exploit.
Best practices for securing PLCs:
There are several best practices for securing PLCs. One of them is network segmentation, which can help protect against cyber-attacks by separating critical systems from non-critical systems. This can help prevent attackers from gaining access to critical systems by first compromising non-critical systems.
Another best practice is access control, which can help prevent unauthorized access to PLCs. This can be achieved through the use of strong passwords, multi-factor authentication, and the principle of least privilege, where users are only granted the minimum level of access necessary to perform their job functions.
Next best thing to do while securing PLCs is restricting the third-party interference. It is strongly advised that the types of connections and data that are available for third-party interfaces be limited in order to strengthen the security of PLCs. It is necessary to specify and limit the various connections and data interfaces before allowing other parties to read and write data for the necessary data transmission.
By implementing these best practices, organizations can improve the security of their PLCs and better protect against cyber threats.
Case study of PLC security breaches
As mentioned in this blog earlier, failing to secure the PLCs of your industry can cause unprecedented damage to the operations and the company’s productions. Here’s a case with a similar incident which happened in 2019-2020, where a petrochemical industry from the Middle East faced a breach to its security, and thus, resulted in attacks on the PLCs.
A PLC at the petrochemical plant in the Middle East was targeted by the virus known as “Triton” in 2020, leading to the closure of the plant’s safety systems. A special form of malware called Triton is made to target industrial control systems (ICS).
Importance of continuous monitoring: Detecting anomalies and potential cyber threats
Continuous monitoring is an important aspect of securing PLCs. By continuously monitoring the activity on the control system network, organizations can detect anomalies and potential cyber threats in real-time. This can help organizations respond quickly to potential security incidents, reducing the impact of an attack.
Anomalies can include unusual network traffic patterns, failed login attempts, or unauthorized changes to system configurations. By detecting these anomalies, organizations can identify potential cyber threats and take appropriate action to mitigate the threat.
Continuous monitoring can also help organizations identify vulnerabilities in their systems and take proactive measures to address them before they can be exploited by attackers. This can include applying security patches, updating firewall rules, or implementing additional security controls.
Conclusion
In conclusion, it is essential to have robust PLC security measures in place to protect against potential threats. This includes implementing best practices such as network segmentation, access control, and patch management, as well as continuously monitoring for anomalies and potential cyber threats.
Talk to us today! Reach us on automation@enwps.com